Effective supplier evaluation helps companies run efficiently. Clear and transparent supplier assessments improve product quality, reliability, and operations. Our comprehensive guide shows you how to find and partner with suppliers that match your requirements.
Key Takeaways
Focus Area | Method |
---|---|
Supply Chain Visibility | Maintain supply chain oversight and tracking |
Assessment Standards | Monitor quality, cost, delivery, innovation, sustainability |
Review System | Apply systematic assessment methods |
Digital Solutions | Use sourcing platforms and analytics |
Collaboration | Keep open supplier communication for improvements |
1. Supply Chain Visibility
Supply chain visibility involves transparent operations between companies and their suppliers. This practice includes monitoring supply chain activities and tracking products throughout their lifecycle. Such transparency strengthens relationships, reduces risks, maintains compliance, and supports company reputation.
2. Assessment Standards
A well-structured supplier evaluation system examines multiple aspects of supplier capabilities. Companies should assess quality standards, financial health, and delivery reliability as primary factors. Additional considerations include technical capabilities, environmental practices, required certifications, and potential for growth. Procurement teams can integrate these requirements into a comprehensive assessment framework.
3. Systematic Assessment Method
The supplier selection process follows a methodical approach. It begins with identifying business requirements and developing assessment questions. This is followed by preliminary reviews and in-depth evaluations. The process continues with on-site assessments, reference validations, and risk reviews before reaching the final selection decision.
4. Digital Assessment Tools
Modern technology has transformed supplier assessments. Companies now utilize sourcing platforms and performance tracking systems for better evaluation. Analytics software provides data-driven insights, while supply chain tracking systems offer real-time monitoring capabilities. Smart automation tools streamline the entire assessment process.
5. Balanced Selection Process
Creating fair supplier assessments requires a multi-faceted approach. Organizations should establish multi-department review teams and implement standard scoring methods. The process should include verification steps, written records, and systems for providing constructive supplier feedback.
6. Supplier Communication
Effective communication forms the foundation of successful supplier relationships. Organizations should establish written expectations and regular input systems. Regular performance discussions help maintain alignment, while online collaboration tools facilitate smooth interaction. Maintaining process clarity ensures all parties understand their responsibilities.
7. Strong Supplier Partnerships
Building lasting relationships requires a strategic approach. Companies should focus on developing partnership approaches and implementing joint improvement projects. Growth programs and business forecasting help align future goals. Recognition systems acknowledge and reinforce positive supplier performance.
8. Problem Management
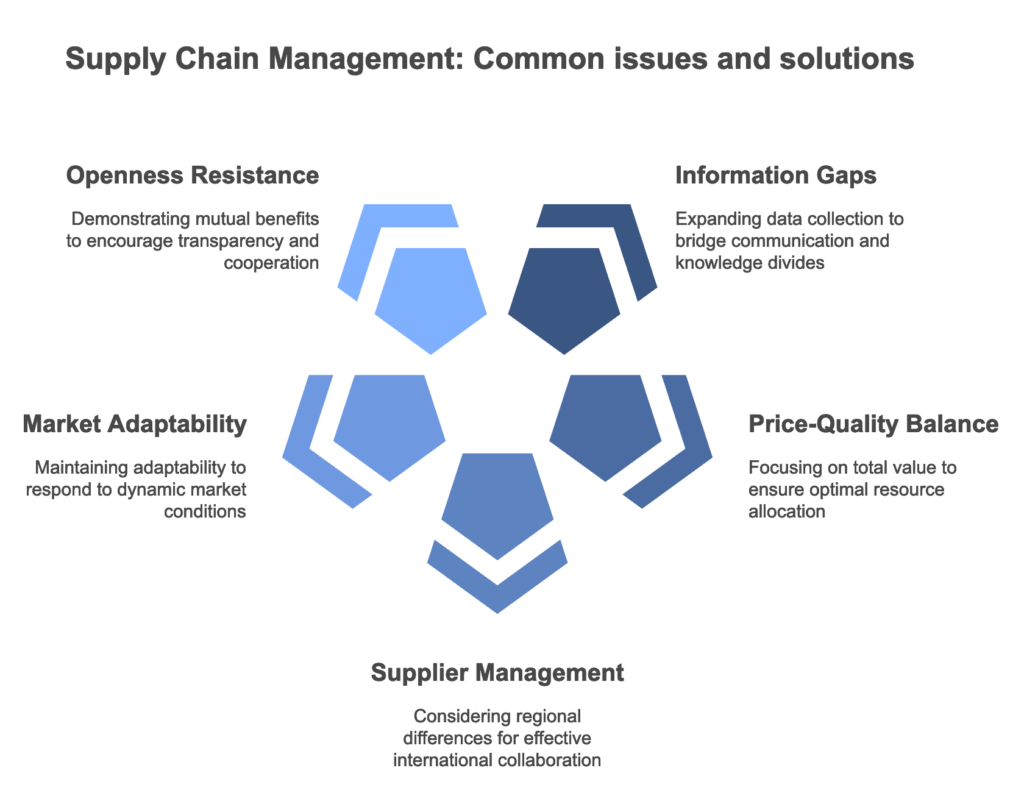
Supply chain management faces several common challenges. Information gaps can be addressed through expanded data collection efforts. The price-quality balance requires a focus on total value rather than just cost. International supplier management needs consideration of regional differences. Market shifts demand adaptable strategies, while resistance to openness can be overcome by demonstrating mutual benefits.
Common issues and solutions include:
- Information gaps: Expand data collection
- Price-quality balance: Focus on total value
- International supplier management: Consider regional differences
- Market shifts: Maintain adaptability
- Resistance to openness: Show mutual benefits
Real Results
Manufacturing Success
A production company implemented analytics tools to track supplier shipments. This resulted in a 15% reduction in wait times and a 10% increase in timely deliveries.
Technology Industry Progress
A tech firm established comprehensive feedback systems, leading to a 20% increase in supplier innovations and a 30% reduction in quality problems.
Essential Elements of Supplier Assessment
Successful supplier assessment relies on four main components. First, organizations must establish clear performance standards for consistent evaluation. Second, a structured process ensures fair and thorough assessments. Third, digital tools provide accurate measurement and tracking capabilities. Fourth, regular supplier communication maintains alignment and encourages continuous improvement.
- Clear Standards: Set specific performance measures
- Organized Process: Follow consistent evaluation steps
- Digital Tools: Apply technology for accurate assessments
- Open Discussion: Maintain regular supplier contact
Creating Better Supply Networks
Transparent supplier assessment supports reliable supply networks. Organizations achieve optimal results by implementing specific standards, organized processes, and appropriate tools while maintaining open communication. Regular system updates enable companies to adapt to business changes effectively.
These proven methods strengthen supplier partnerships, minimize operational problems, and generate improved business results. Additionally, they support responsible and sustainable supply chain practices across the entire network.